Healthcare forms a critical aspect of societal life,
yet the current healthcare system is under tremendous strain. Overall, the healthcare system is intricate and involves many different departments with varied, yet interconnected roles. Most healthcare practices have remained consistent over time and this lack of progression in terms of streamlined processes often leads to loss in terms of time and money.
It has been observed that approximately 30-50% of healthcare works can be considered as waste, which ultimately lead to overspending and lack of progress.
Implementation of the lean six sigma methodologies in healthcare have proven to be beneficial, but the complexity of the system builds barriers in its implementation. The first step in the lean methodology, however is to identify and cut-out the areas of waste (figure).
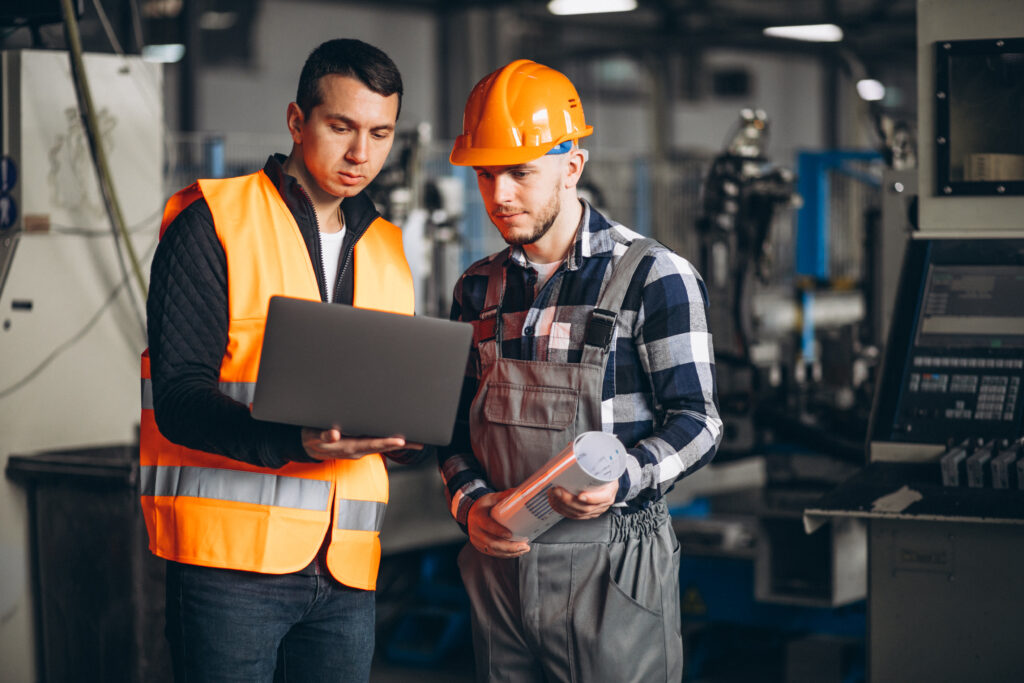
- Waiting or idle time:
Any reason that causes patients or employees to stand by can be considered as waste. For example, sitting in waiting areas, waiting lists for appointments, idle equipment, etc.
- Inventory:
Inventory means tied-up costs and storage space. Surplus of medications, supplies, equipment, paperwork, etc. are all considered as inventory waste.
- Defects:
Lack of protocol, staff not following protocol, system failures, medical or surgical mistakes and even misdiagnosis are considered to be defects in the system since they often lead to loss of quality care and increased cost.
- Transportation:
Unnecessary movement of people, equipment, supplies, etc. from one department to another can be considered as waste. These create delays in care and increase chances of injury.
- Untapped human potential
Consumption of employee’s time due to waiting, defects, overprocessing, imbalanced work flows, etc are considered as a waste, since this time is unproductive and also has a negative impact on the morale of the employees.
- Over-processing
Unnecessary work towards treating a patient amount to overprocessing. These include needless tests, paper work, data entry on more than one system, etc.
- Over-production
Overproduction includes creating too much of something or creating something at an inappropriate time. For example, preparing medication trays for patients to be discharges, test duplication, extending hospital stays, etc.
- Motion
Waste in motion occurs when a hospital employee performs movements within their workspace that does not add value to the patients. For example, bending or reaching for supplies, increased steps due to poorly designed interiors, poor patient transportation processes like transfers between beds, bed to wheel chair or bed to operating table.
A lot has changed and improved in the healthcare space since the first pioneers of ‘lean’ shared their learnings in 2007 at the Global Lean Healthcare Summit. However, a lot more changes are needed to adapt the lean methodologies into healthcare so as to gain control over costs while improving quality care given to patients.
Reference: NEJM Catalyst. 2018. Available [Online] at: https://catalyst.nejm.org/doi/full/10.1056/CAT.18.0193 Accessed 20 Dec 2022