Small and medium enterprises (SMEs) contribute substantially
towards the growth and development of a country and the number of SMEs is constantly increasing. Lean Six Sigma (LSS) can provide a powerful solution for SMEs looking to streamline their operations and reduce waste.
The current economic environment requires cost reduction, output of a high quality product, reduced delivery times and high levels of customer satisfaction. Lean six sigma has always been a most powerful strategy used across industries to improve organisational processes and reap rich rewards in terms of efficiency and productivity
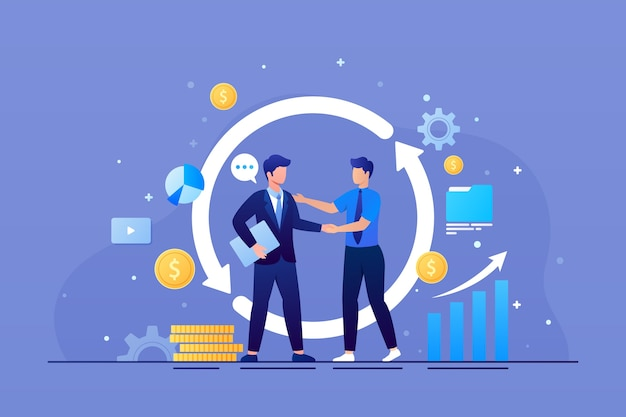
By focusing on strong leadership, employee involvement, clear goals and objectives, a data-driven approach, process improvement, measurement and tracking, and ongoing training and development, SMEs can ensure the success of their lean six sigma implementation and drive positive results for their business.
But SMEs face unique challenges when it comes to improving their processes and increasing efficiency. Some of the challenges are listed below –
- Low number of units, therefore low volume of production
- Lack of infrastructural facilities
- Greater competition (compared to large and established businesses)
- Higher prices of base ingredients
- Unavailability or lack of skilled labour
- Inability to retain talent due to lack of ability to pay as per competition
- Smaller resource allocation towards training
Implementation of lean six sigma can provide a powerful solution for SMEs looking to improve their processes and increase efficiency.
Here are some ways in which SMEs can integrate the benefits of lean six sigma –
- Strong leadership:The implementation of lean six sigma requires strong leadership and a commitment from the top. The leadership team must understand the importance of lean six sigma and be willing to invest the time and resources necessary to ensure its success.
- Ensuring employee involvement: Employees play a critical role in the implementation of lean six sigma. SMEs must engage their employees and involve them in the process to ensure their buy-in and support.
- Setting clear goals and objectives:SMEs must have clear goals and objectives for their lean six sigma implementation. This will help focus their efforts and ensure that they are using lean six sigma in the most effective way possible.
- Data-driven approach:Lean six sigma is a data-driven methodology. SMEs must have a strong data collection and analysis process in place to ensure the success of their lean six sigma implementation.
- Focus on process improvement:Lean six sigma is about improving processes, not just fixing problems. SMEs must have a focus on continuous process improvement to ensure that they are making the most of their lean six sigma implementation.
- Measurement and tracking:SMEs must measure and track their progress to ensure that they are making real progress towards their goals and objectives. This will also help identify areas for further improvement.
- Ongoing training and development:Lean six sigma is an ongoing journey, not a one-time event. SMEs must invest in ongoing training and development for their employees to ensure that they are continuously improving and making the most of their lean six sigma implementation.